Any Welders in the house?
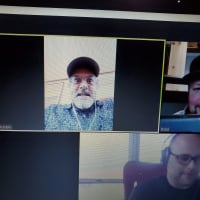
So I am going to basically teach myself how to weld. I am going to be starting on my trailer smoker here soon and want to do it myself to have the satisfaction of me building it, make the necessary changes I need to as I go and save on cost. I will probably build the trailer from scratch and will be using a 500gal propane tank as the main cook chamber on the smoker, something like a 125gal for a charcoal grill on the back side. I am looking into buying a welder and am liking something like the Lincoln Electric Power Mig 180c. Seems like it should be able to handle the material as I believe the thickest I will be using on the project will be 3/8" steel for the firebox.
What I want to get a feel for is, does anybody have experience with this welder or something similar they can point me to. I am leaning towards flux core welding to avoid having the shielding gas in my home garage where I will be building this. From what i know the flux core may not be as nice of looking welds as a gas however it is cable of welding thicker material without the 2nd pass.
What I want to get a feel for is, does anybody have experience with this welder or something similar they can point me to. I am leaning towards flux core welding to avoid having the shielding gas in my home garage where I will be building this. From what i know the flux core may not be as nice of looking welds as a gas however it is cable of welding thicker material without the 2nd pass.
Team O'Donnell FTW!
"I've got a great cigar collection - it's actually not a collection, because that would imply I wasn't going to smoke ever last one of 'em." - Ron White
"I've got a great cigar collection - it's actually not a collection, because that would imply I wasn't going to smoke ever last one of 'em." - Ron White
0
Comments
I never welded for a living, but worked where there were dozens of 'em. So I'd ask them for tips, and weld up my government jobs during my lunches. Stick welding is a bit more difficult, but way more fun once you get the hang of it.
"I've got a great cigar collection - it's actually not a collection, because that would imply I wasn't going to smoke ever last one of 'em." - Ron White
At any given time the urge to sing "In The Jungle" is just a whim away... A whim away... A whim away...
Stick with MIG, at least at first. You shouldn't need the flux-core, "inner-shield" is what we used to call it, if it's still the same, unless you're welding really thick stuff. Like more that 1/2 inch metal. Also, the flux core produces more noxious gasses than the MIG tank will. Stick (arc) welding takes time and practice. I like it better, but, time and practice.
When my Son built his Mustang he called and asked me to teach him to weld, over the phone. My advice to him was MIG, get a bunch of scrap metal of different thicknesses from some local iron working shop, machine shop etc., then practice different settings. Once you've gotten those practice welds looking good, you should be ready.
Remember to tack (tiny weld) your whole piece together before you start welding in earnest, both because you may need to start over, and because the cooling weld pulls the metal and will distort what you're trying to do. Also, if you weld galvanized metal it will release iso-cyanide gasses and precipitate. Nasty stuff, poisoned my sinuses.
Good luck.
"If you do not read the newspapers you're uninformed. If you do read the newspapers, you're misinformed." -- Mark Twain
"I've got a great cigar collection - it's actually not a collection, because that would imply I wasn't going to smoke ever last one of 'em." - Ron White
Should you decide on arc welding, the easiest rod to master is the 7014. Technically it's an "all-position" rod, but you're best off not trying verticals or overhead with it until you're pretty good, and by then you'd be able to use other rods that will do those jobs better.
The numbers tell you about the rod and the flux on it. The first 2 (or sometimes 3) numbers indicate the metal strength. 70 means 70,000lbs per sq in tensile strength. the 1 means all position, a 2 means flat only. The 4, in this case means it's a "Jet rod", you can lay in at the proper angle and simply feed it into your work without having to learn movement patterns, back and forth etc. that you might use with, say, a 6011 (penetrating) rod.
Typically, if I were doing your project, on all the thicker pieces I would tack everything with a 6011, maybe do a deep pass with it, then cover with a 7014. Areas prone to vibration I'd use a 7018, which is, overall, my favorite. Takes practice, though.
"If you do not read the newspapers you're uninformed. If you do read the newspapers, you're misinformed." -- Mark Twain
Totally agree with @Amos_Umwhat
Most of my welding is Mig or 7018 stick. 75% of everything I weld is done with wirefeed.
I prefer gas shielded using 75/25 argon/co2 gas. I only use innershield/flux core when I am out in the field, but even then will grab the 7018 rod most the time.
If you plan on painting or poweder coating, the gas shielded wirefeed will save tons of prep work.
Money can't buy happiness, but it can buy cigars and that's close enough.
"I've got a great cigar collection - it's actually not a collection, because that would imply I wasn't going to smoke ever last one of 'em." - Ron White
http://www.custompits.com/mini-beast-pro
"I've got a great cigar collection - it's actually not a collection, because that would imply I wasn't going to smoke ever last one of 'em." - Ron White
Money can't buy happiness, but it can buy cigars and that's close enough.